Routing cables/hoses for water-cooled system
Adopt one of the following procedures, depending on whether the rack is in a raised-floor environment.
- Install filler panels over all unoccupied bays.
- Route signal cables at the rear of the rack so that they enter or exit the cabinet through the top and bottom air baffles.Figure 1. Managing cables with the upper air baffleFigure 2. Managing cables with the lower air baffle
- Bundle signal cables together in a rectangle so that the air-baffle sliders are closed as far as possible. Do not bundle signal cables together in a circular formation.
Raised-floor environment
The following illustrations show routing and securing the hoses in a raised-floor environment for individual racks and adjacent racks.
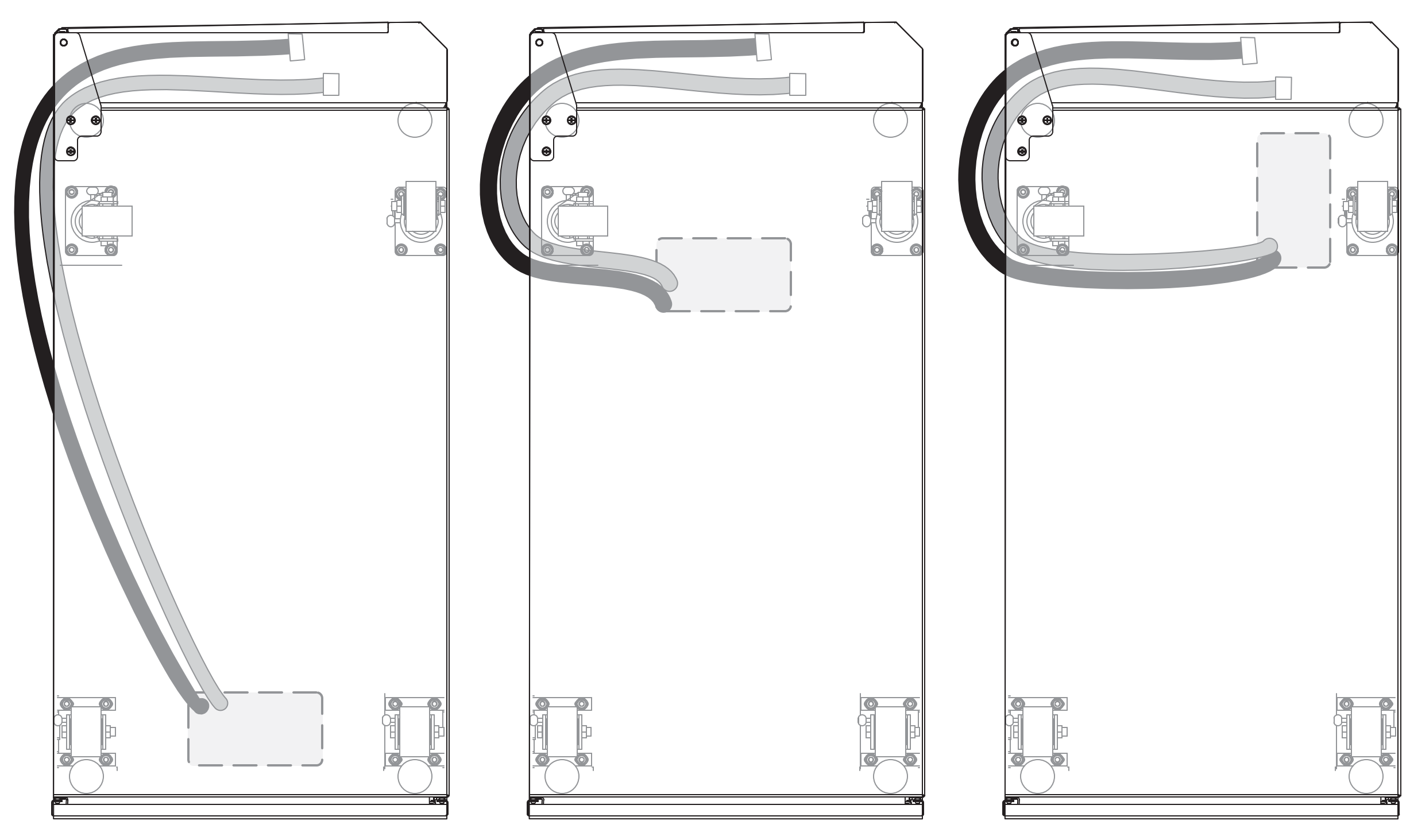
In the following illustration, the numbers represent the suggested placement of racks that share one hole in the floor. For example, if three racks will share one hole in the floor, place the racks as shown by the numbers 1, 2, and 3. If you want to add a fourth rack that will share the same hole in the floor, place it next to rack number 1.
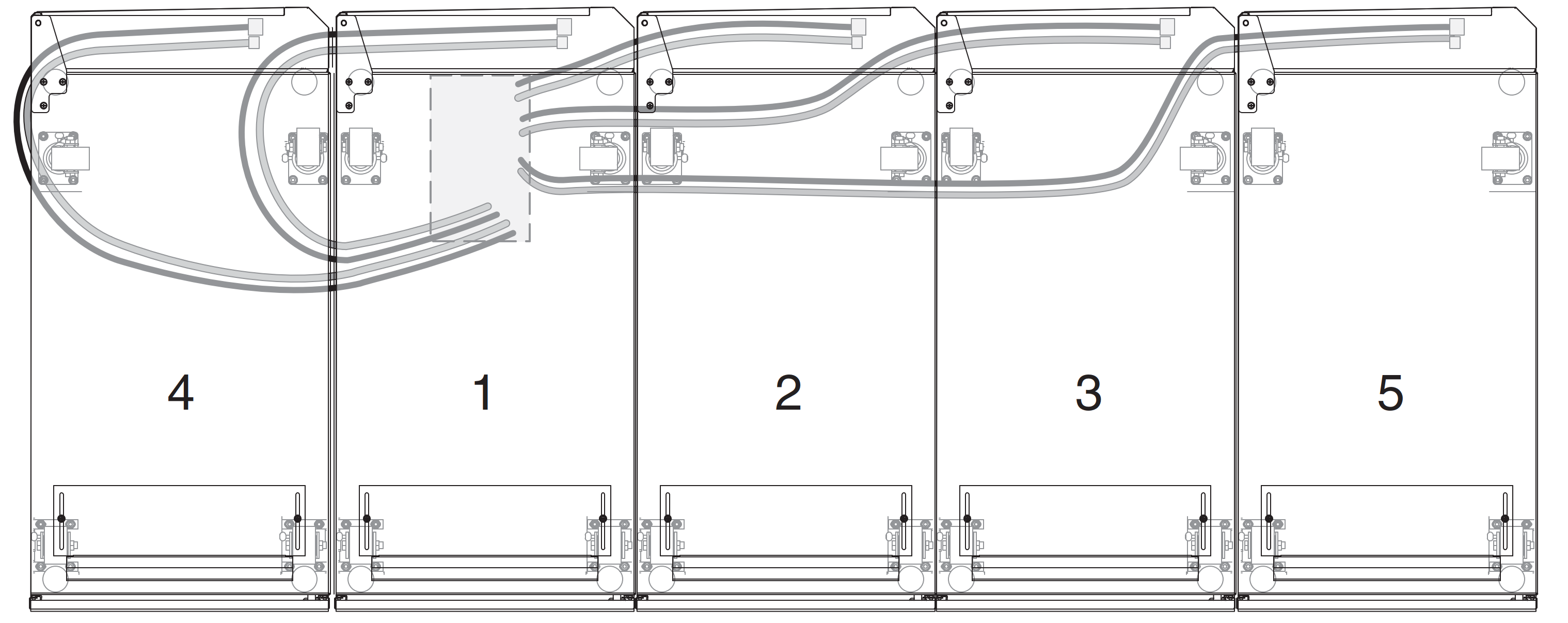
To route and secure the hoses in a raised-floor environment, complete the following steps:
Raised-floor and non-raised-floor environments
If the coolant distribution unit (CDU) that is providing water to the heat exchanger is in a row of racks with heat exchangers, all hoses can be routed on the floor, irrespective of if it is a raised floor or slab installation. The Type 7D6E rack has sufficient clearance underneath the rack to enable the ball valves to be run underneath the rack. This provides a very clean hose-routing solution with hoses of minimum length.