Install the carrier base board (CBB)
Use this information to install the carrier base board (CBB). This procedure is trained technician only.
About this task
Required tools
Make sure you have the required tools listed below in hand to properly replace the component.
Water loop kits
SD650-I V3 Water loop service kit (03KH870)
SD650-I V3 Water loop putty pad kit (03LD670)
Screws and screwdrivers
Prepare the following screwdrivers to ensure you can install and remove corresponding screws properly.Screwdriver Type Screw Type Torx T10 head screwdriver Torx T10 screw Phillips #1 head screwdriver Phillips #1 screw Phillips #2 head screwdriver Phillips #2 screw
To identify the gap pad/putty pad location and orientation, see Gap pad and putty pad identification and location.
Before replacing the gap pad/putty pad, gently clean the interface plate or the hardware surface with an alcohol cleaning pad.
Hold the gap pad/putty pad carefully to avoid deformation. Make sure no screw hole or opening is blocked by the gap pad/putty pad material.
Do not use expired putty pad. Check the expiry date on putty pad package. If the putty pads are expired, acquire new ones to properly replace them.
Read Installation Guidelines and Safety inspection checklist to ensure that you work safely.
Turn off the corresponding DWC tray that you are going to perform the task on.
To avoid damaging the water loop, always use the water loop carrier when removing, installing or folding the water loop.
- When removing the new carrier base board from the package box,
Hold the long sides of the carrier base board with two hands.
- Make sure to hold the carrier base board gently. Avoid applying pressure or force to it.
- When installing the carrier base board to the node, avoid touching the connectors on the carrier base board. Be careful not to damage any surrounding components inside the node.
Figure 1. Removing carrier base board from the package box Once the carrier base board is removed from the plastic protective bag, hold two handles with both hands to move the carrier base board.
Figure 2. Removing carrier base board from the package box
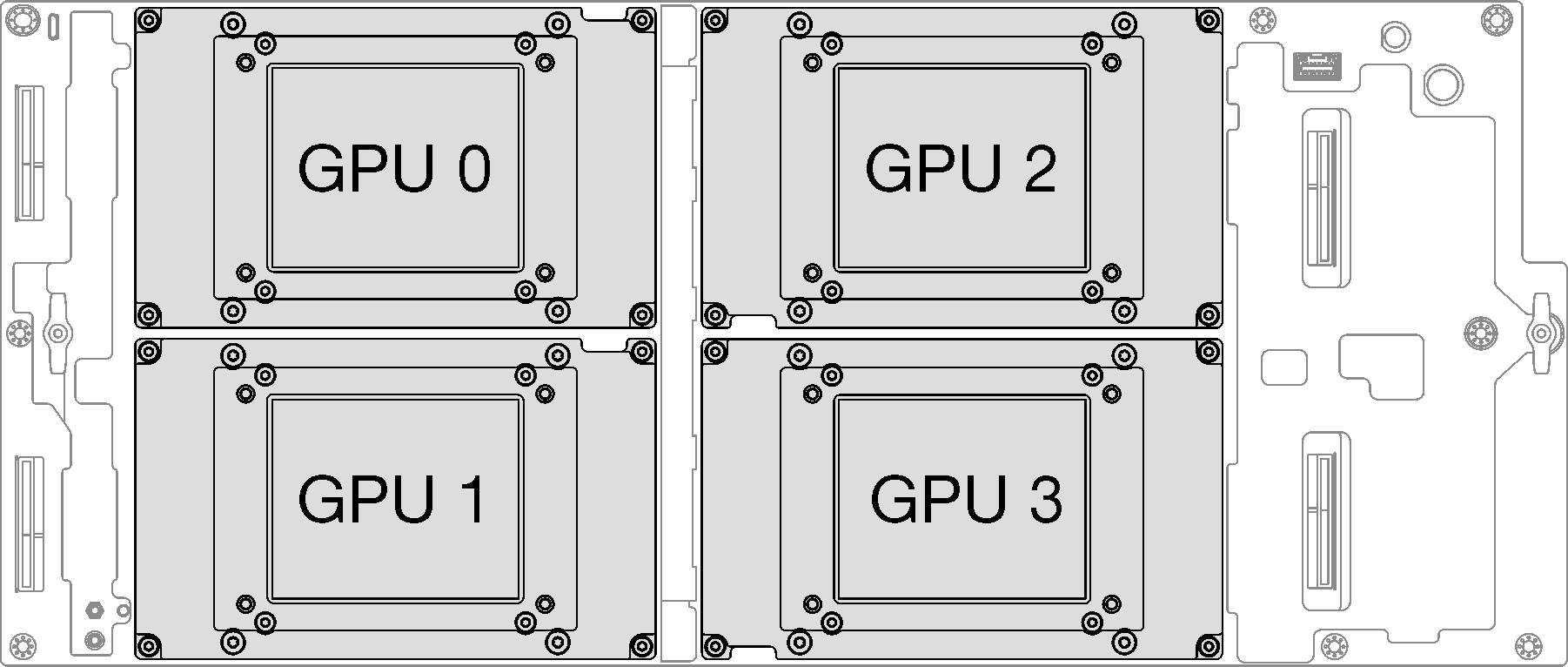
Requirements for proper CBB installation
- Update Retimer firmware via XCC Web GUI or LXCE OneCLI with the following command, where FW_FILE_NAME is the Retimer firmware file name.
OneCli update flash --forceid FW_FILE_NAME --checkdevice --dir /flash/ --output /flash/result
After updating Retimer firmware, reboot the system.
Update carrier base board firmware by updating XCC firmware, see Lenovo XClarity Controller portal page.
After updating XCC firmware, perform virtual reseat to optimize system, see SMM2 User Guide.
Go to Drivers and Software download website for ThinkSystem SD650-I V3 to see the latest firmware and driver updates for your server.
Go to Update the firmware for more information on firmware updating tools.
Procedure
Make sure to follow Gap pad/putty pad replacement guidelines.
Make sure to follow Gap pad/putty pad replacement guidelines.
Connect and route the cables in the tray. See GPU node cable routing.
Install the cross braces. See Install the cross braces.
Install the tray cover. See Install the tray cover.
Install the tray into the enclosure. See Install a DWC tray in the enclosure.
- Connect all required external cables to the solution.NoteUse extra force to connect QSFP cables to the solution.
Check the power LED on each node to make sure it changes from fast blink to slow blink to indicate all nodes are ready to be powered on.
After installing the CBB, it is required to update carrier base board firmware (included in XCC firmware) and Retimer firmware. Latest firmware can be found at Drivers and Software download website for ThinkSystem SD650-I V3.
- Update Retimer firmware via XCC Web GUI or LXCE OneCLI with the following command, where FW_FILE_NAME is the Retimer firmware file name.
OneCli update flash --forceid FW_FILE_NAME --checkdevice --dir /flash/ --output /flash/result
Update carrier base board firmware by updating XCC firmware, see Lenovo XClarity Controller portal page.